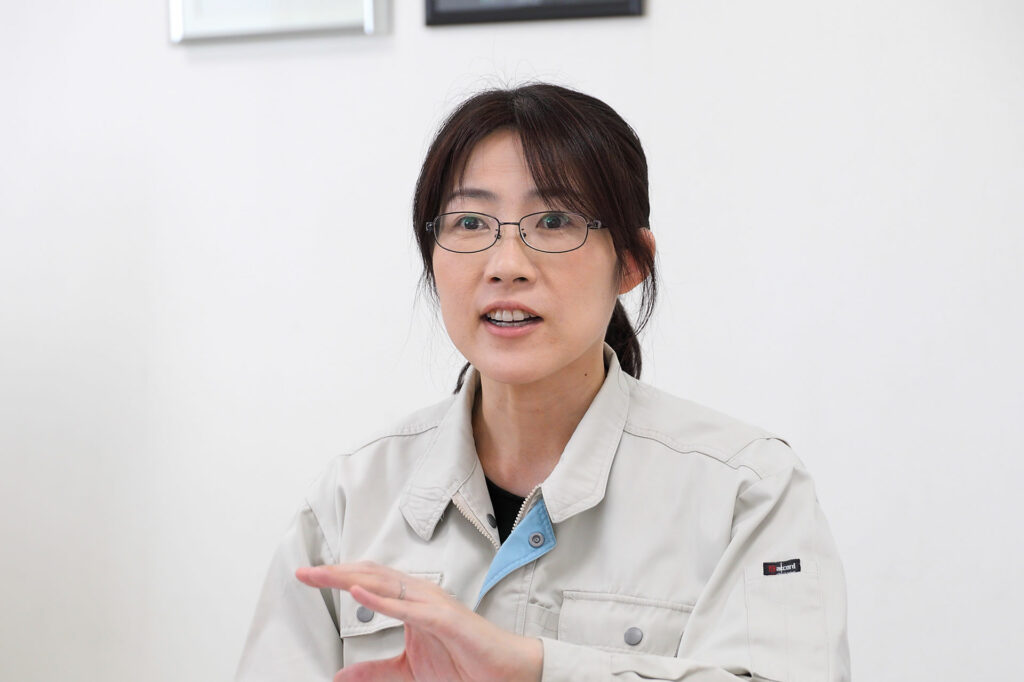
【事業の現在】
精密ギヤポンプを造れるメーカーは
国内に2社
ギヤの回転によって、水や油、高温で流体状になった樹脂素材を定量で連続して送り出すギヤポンプという製品がある。押出成形や化学合成繊維などのラインに不可欠で、1本が1ミクロン単位の極めて細く・均一な糸製造において、最も重要な樹脂流量を制御する機構がギヤポンプであり、非常に高い流量精度を要求される。そうした精密ギヤポンプを造れる数少ない1社が協和ファインテックだ。
「もともと大手繊維メーカーの協力会社としてスタートしたので、1975年にはもうギヤポンプを独自開発しました。繊維業の主力が海外に移っても、当社は糸づくり・ギヤポンプというコア技術を磨いてきました。その蓄積が、精密ギヤポンプのベースになっています」
と語るのは、品質保証部課長で、社長の姉でもある植田佳代子氏だ。
1ミクロン単位の細く均一な糸を製造する場合、送液する素材の温度、粘度、圧力、送液スピード、耐薬品性、耐摩耗性など、様々な要素に合わせたベストな選定が必要で、既成品のラインナップでは対応しきれないことが多い。同社は、培った経験を元に、顧客の要求品質に合わせたベストなギヤポンプを一から設計し提案する。
「ギヤポンプは意外な広がりを見せています。例えば光ファイバーやセラミックコンデンサなど、現在のデジタル通信・家電の分野を支える根幹でギヤポンプが活躍しています。他に医療、自動車、さらに世界が開発を競う全固体電池にも精密ギヤポンプが活用できると注目されています」
と代表取締役社長・橋本宗幸氏は笑う。
【将来の方向性】
主要4事業を展開。その大半の製品を
オーダーメイドで自社開発
精密ギヤポンプ事業以外にも、同社には3つの柱がある。その1つが化合繊設備だ。創業以来の事業だが、今は様相を大きく変えている。
「今の主流は、単純な糸ではなく高性能繊維。おむつなどの吸湿繊維や、防護服などの切れない服。あるいは飛行機にも使われる炭素繊維など。それとフィルタですね。中空糸というチューブ状の糸で、チューブの内から外、外から内へ移動するとき、必要な物質だけを通すフィルタの役割を果たします。医療分野では、透析治療で血液と透析液を置換するフィルタなどで使われています。」(植田氏)
フィルタ技術の転用で生まれたのが、環境装置事業。活性炭フィルタの働きで空気中の揮発性有機化合物(VOC)やアルコール類などを回収するもので、有機溶剤を使用する業界ではこうした設備が欠かせない。
最後の1つが医療機器だ。透析治療で使うフィルタの製造設備を同社が作っていたという接点から、大手医療機器メーカーと協力し、人工透析機を開発。海外向けに供給している。
「当社は、従業員数約160名のうち設計技術者が40数名と、ありえないほど多くの人員を設計部門に配置しています。と言うのも、当社が手掛けるのはほとんどが自社開発のオーダーメイド品ばかりだから。あまり儲かるビジネスモデルとは言えませんが、独自技術を磨いてきたからこそ、4つの事業が生まれ、各部門が順調に伸びているのです」(橋本氏)
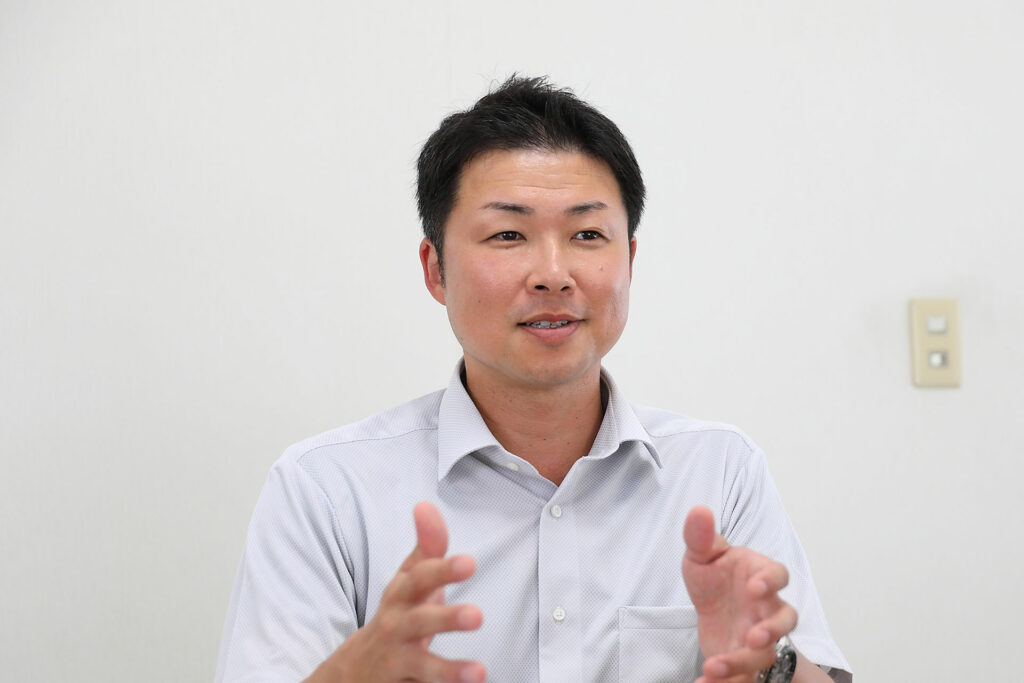
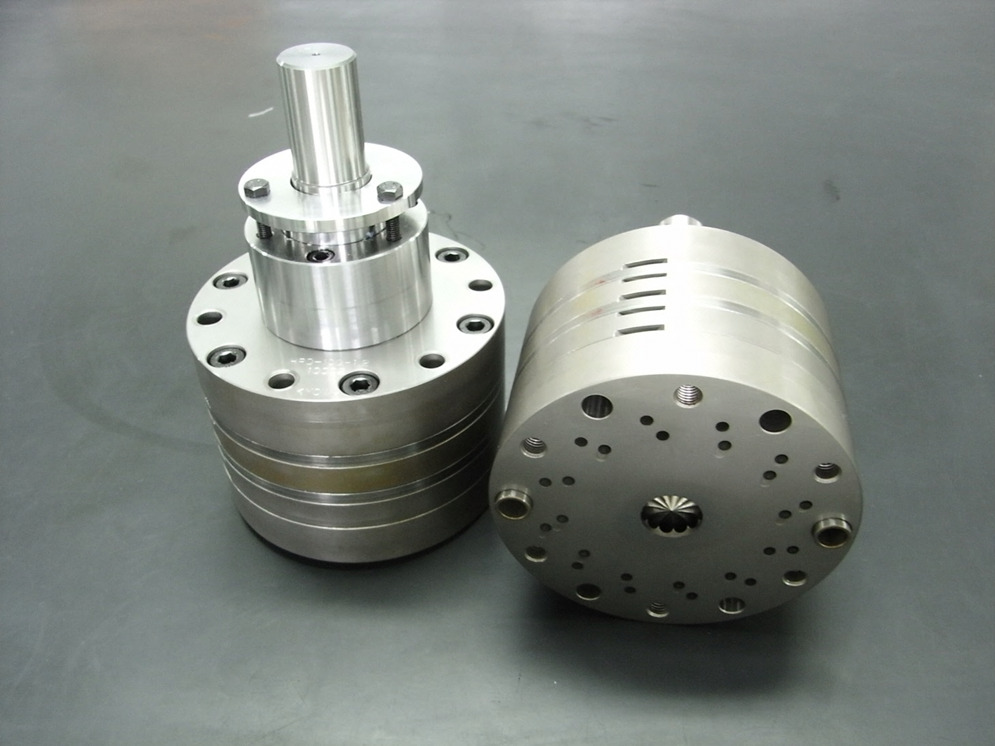
【働き方改革】
全員が同じ視野・価値観で進むため
ミッション・ビジョン・バリューを共有
精密ギヤポンプ・樹脂成型設備という技術をコアに、事業を大きく広げる同社。しかし枝葉が広がるほど、全体の方向性を見失いがちだ。そこで同社は、従業員全員の目線を合わせるため、ビジョン・ミッション・バリューを設定した。
「各部から参加した従業員に私も加わり、思いを共有しました。そして“お客様の課題を解決することが、社会貢献につながる”というコンセンサスが生まれ、目指す方向が明確になりました」
と橋本氏は言う。そうやって【糸から環境、医療、さらには宇宙まで、ビジネスチャンスを創造し続ける総合機械メーカーを目指します】というビジョンと、【私たちは、社会や企業の課題解決を通して、みんなの幸せを形にする機械を作り続けます】というミッションを決定。社内の浸透を図っている。
関連して、社内コミュニケーションの充実も進める。
「部門・拠点内だけに存在する“固有の慣習”という弊害をなくそうと、社内横断型の委員会を作ることから始めて、2020年1月にはWEB会議システムを用意。今では遠方のお客様との打ち合わせや海外製品のチェックにも、このシステムを活用しています」(植田氏)
従業員一人ひとりとの定期面談も実施。面談を充実させるため、主任以上全員のコーチングスキル研修も導入した。
「様々な改革のおかげか、“自分たちには新たな分野を開拓する力がある”と自信を深める従業員が増えてきたように思います」(橋本氏)
同社にはテラヘルツ波という新たな技術領域も芽吹き始めている。医療に、環境に、あるいは宇宙に向け、同社の技術はさらに発展する。
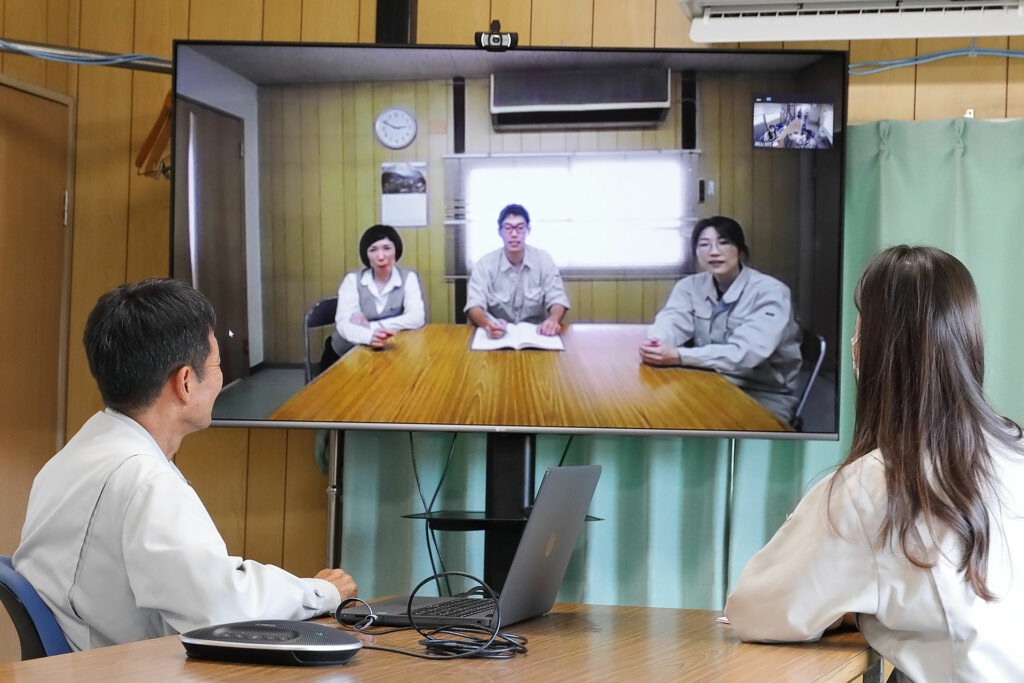
